Gas detection is required in many industries due to safety requirements, insurance needs, and simply for the safety of personnel. Factories and industrial manufacturers, food and beverage companies, fisheries, mining sites, and power stations all depend on having reliable gas detection monitors in place. This generally means calibration, maintenance, and general upkeep are necessary as well. Even state and local governments need gas detection in order for sanitation and other work to be performed safely. Given how frequently gas detection is necessary, it’s understandable that many people would like to know more about gas detection and how monitors operate. This lifesaving science deserves some attention.
Detection
Many gases are always present in the atmosphere. Methane, carbon monoxide, argon, and other gases are generally detectable even if only in trace amounts. Detecting a gas isn’t simply about confirming that it’s present. The amount of gas in the area is crucial. Atmospheric oxygen tends to be around 21%. However, a higher concentration of oxygen could prove to be a fire hazard in certain environments, so the level of oxygen needs to be monitored carefully.
On the other hand, carbon monoxide (CO) tends to be a byproduct and isn’t present in large amounts in the atmosphere. Even at lower levels, carbon monoxide can cause headaches, dizziness, or shortness of breath. At higher concentrations, vomiting and loss of consciousness are possible. Unfortunately, carbon monoxide tends to be a common result when burning fuel. Gasoline, propane, and other instances of combustion tend to release carbon monoxide into the air. Obviously, detection of carbon monoxide becomes absolutely essential in those environments, and workplaces commonly have CO monitors stationed at key locations.
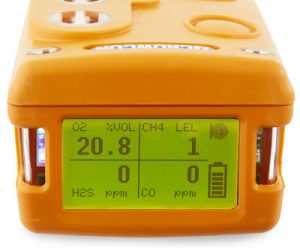
Operation
Gas detectors use sensors to identify the presence of particular gases in the local atmosphere. Since these sensors have to identify a specific gas, there are no “universal” gas detection systems. However, a gas detector may be able to detect multiple gases. For instance, a common 4-gas detector might be designed to identify oxygen (O2), flammable gases or vapors (LEL), hydrogen sulfide (H2S), and carbon monoxide (CO). These 4-gas detectors are quite common when it comes to marine work or ship operations.
Most portable gas detectors rely on a catalytic bead sensor. In order to continue regular operation and avoid the buildup of tar on the ring, these sensors need an environment of at least 10% oxygen. Typically, these sensors last around three years, but they need frequent calibration and bump testing to remain accurate. These devices tend to be sensitive, so they can be damaged if they get dropped.
Infrared sensors are beginning to become much more popular. They can operate in inert atmospheres and don’t require ongoing calibration. Additionally, they’re known to be quite energy-efficient. These infrared-based detectors can last for several years and don’t need the upkeep of catalytic bead sensors, which is a definite advantage.
Benefits
In addition to keeping your personnel safe from harm, gas detection is also able to identify leaks. Leaks often indicate damaged equipment or other possible hazards that may be costly to repair. Catching leaks early saves money and time. In some cases, remedying a leak early could even save property from being harmed or prevent workplace accidents.
Having reliable gas leak detection equipment is absolutely vital, especially if you have a business or work in an industry where gas leaks are an ever-present risk. Contact DOD Technologies, Inc., at 815-680-6086 if you have any questions or if you would like to learn more about this constantly evolving technology.